

McKenna developed the first indexable carbide cutting tools. It's been around for nearly one hundred years but didn't come into widespread use as a cutting tool material until after World War II, when Kennametal founder Philip M. That brings us to tungsten carbide, more commonly referred to as carbide or sometimes cemented carbide. The user must therefore take extra care to align them properly and avoid the radial tool pressures that might occur when drilling into intersecting holes (hydraulic manifolds, for example) and angled surfaces. The only caveat is that cobalt drills, due to their greater hardness, are more brittle than HSS. Cobalt, however, will in most cases last longer than its less wear and heat-resistant cousin, and as we've seen, run much faster besides.
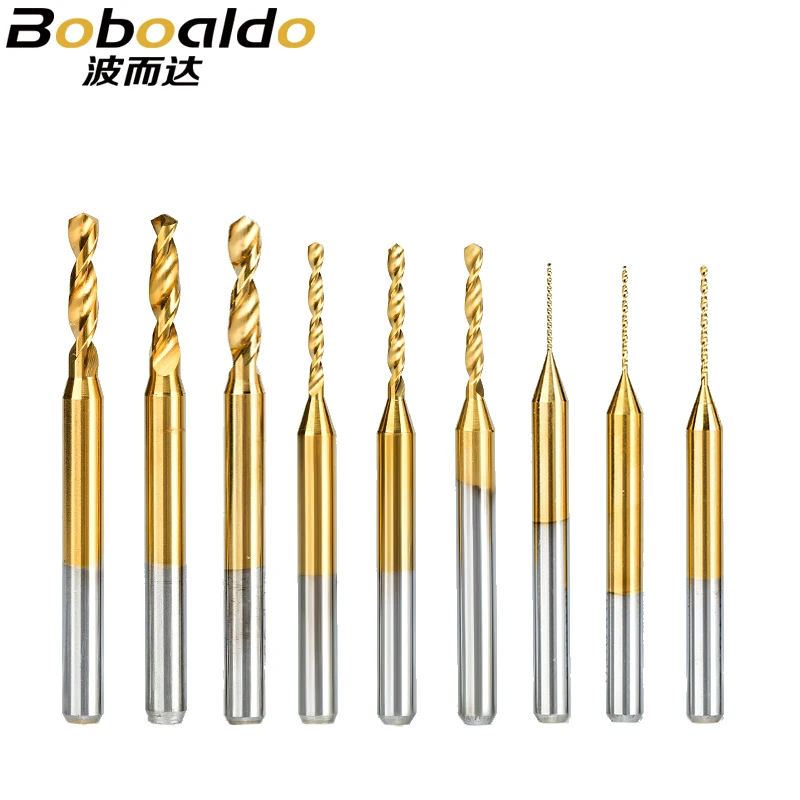
It’s also important to note that, despite what some websites suggest, there’s no such thing as a titanium drill bit (only drill bits coated with one or more of the thin film materials just mentioned).Īs to the question “when should a cobalt drill bit be used," the answer is straightforward: anywhere you would use an HSS drill. This last point is important, since all cutting tools, whether they are HSS, cobalt, or tungsten carbide (more on this shortly), benefit from coating, be it TiN (titanium nitride), TiAlN (titanium aluminum nitride), or one of the other many tool coatings available on the market today. Either way, be sure to follow the cutting tool manufacturer's recommendations. That doesn't seem like much difference, but together with cobalt's greater heat resistance, it supports higher cutting speeds-depending on the brand and whether the drill is coated, this might mean 50% faster spindle RPM and commensurately higher feedrates. Where "regular" M2 HSS comes in at a hardness of around 62 HRC, M35 starts at 65 HRC and M42 measures 67 or so. Read on.Ĭompared to regular M2 tool steel, M35 and M42 are indeed super. Despite their broad popularity, relatively low cost, and excellent mechanical properties, you’ll soon see why HSS and its cobalt counterparts aren’t always the best cutting tool materials for your drilling application. It’s this last group, HSS, that we’re here to discuss today, along with that most widely used of all cutting tools, the drill bit. These include D2, A2, H13, S7, and other tough, heat-treatable, and wear-resistant metals used to make everything from plastic injection molds to stamping dies to high-speed steel (HSS) cutting tools. This list is by no means complete, but we’d be remiss in not tagging a few members of the tool steel family. Steel and all its many alloys-stainless among them-range from “cuts like butter” to “why do I keep breaking tools?” There’s soft, stringy aluminum and polymers like ABS, Nylon, and Teflon.Ĭast iron is relatively abrasive but nowhere near that of glass and fiber-filled composites. Nickel-based superalloys like Inconel and Hastelloy are called “super” for a reason. Machine shops, maintenance personnel, and the manufacturing community overall face off against a veritable universe of different materials each day:
